Medical Device Prototyping and Manufacturing
Medical device prototyping and rapid manufacturing are the foundation of your medical product design and development process. You can send these prototype parts and low-volume production parts to the lab or clinical trials and ultimately to market faster.
Role in medical devices
Importance of Prototyping and Rapid Manufacturing in Medical Device Development
Prototyping and rapid manufacturing (RPM) are essential tools for medical device developers. These techniques allow designers to test their designs before investing significant time, money, and resources into production. By creating prototypes, developers can identify potential issues early on, such as design flaws or material compatibility problems that could prevent the product from being approved by regulatory agencies. This allows them to make necessary changes before proceeding with full-scale production, reducing costs and improving efficiency. Rapid manufacturing also offers several advantages over traditional manufacturing methods. It enables companies to produce small quantities of products quickly without incurring high overhead costs associated with large-scale productions. Additionally, RPM allows for customization of medical devices based on individual patient needs, which is crucial in today's healthcare landscape where personalized medicine is becoming increasingly popular.
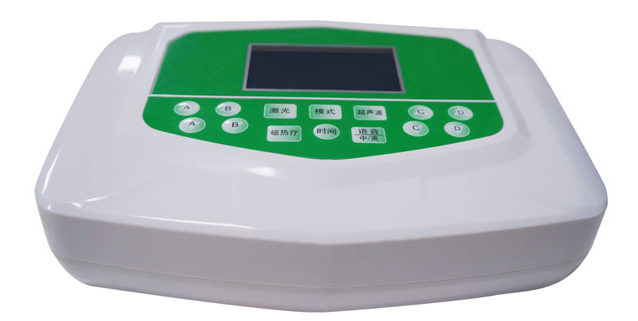
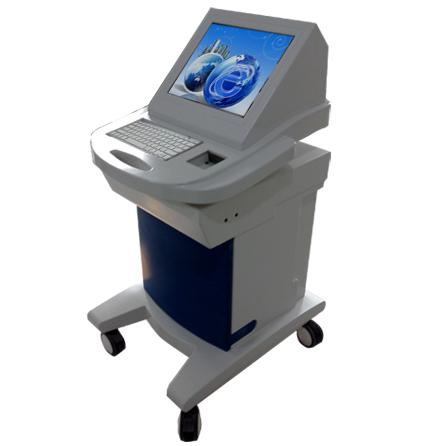
Best Practices Supported by Medical Device Prototyping and Manufacturing
Medical device prototyping and manufacturing involves complex processes that require careful attention to detail. To ensure the safety and effectiveness of medical devices, you need to pay attention to:
1. Comply with regulatory requirements: Medical devices must comply with various regulations such as the US Food and Drug Administration (FDA) or the EU Medical Device Directive (MDD). These regulations set strict guidelines for the design, testing, and manufacturing of medical devices.
2. Quality control measures: Manufacturers implement quality control measures to ensure that their products meet high standards of performance and safety. This includes thorough testing and validation at every stage of the production process, from design to final assembly.
Dedicated to the Development and Manufacture of Medical Devices
Oakon offers a full range of rapid prototyping and manufacturing solutions to the medical industry. From surgical tools to large-scale treatment units, our engineering approach will help you move from your initial idea to a realistic plan.
Medical Device Prototyping and Medical Parts On-Demand Manufacturing Provided by Oakon
Lead You from Prototype to Production with Our Successful Experience
With years of experience, Oakon specializes in medical device prototyping and medical parts machining and has served many medical device manufacturers around the world. We will help you every step of the way, from the first prototype, through testing and iterations, to new product demonstrations, and even short or low volume production runs.
Our prototyping and manufacturing capabilities include a fully equipped in-house CNC machining and finishing shop, 3D printing, urethane casting, and rapid injection molding to cover all your medical device development needs.
Medical Device Enclosures, Custom Machined Plastic Housings
Medical device enclosures and custom machined plastic housings are important components in the medical industry because they provide a secure and protective environment for medical devices.
Enclosures protect medical devices from environmental factors such as moisture, dust, and contamination, which can affect their performance and reliability. They also help to prevent damage or loss of sensitive data during transportation or storage.
Custom-machined plastic housings are designed specifically for a particular medical device and are often used to ensure compatibility with other components within the device. This ensures that the entire system functions smoothly and effectively without any potential conflicts or issues.
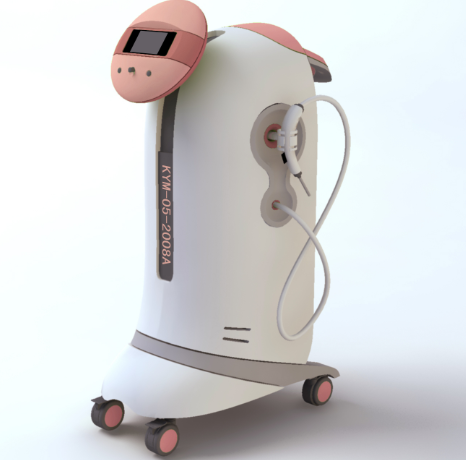
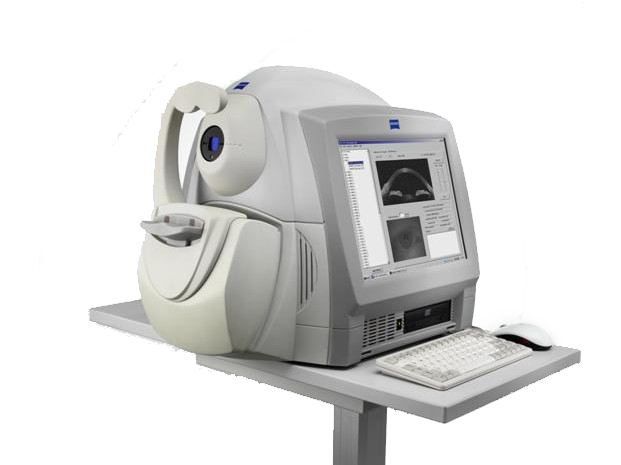
Surgical Instruments and Surgical Tools, Precision CNC Machining for Medical Components
Use of computer numerical control (CNC) technology in the manufacturing of medical devices and components. CNC machines are highly automated and can be used to create complex shapes and structures with high precision and accuracy.
In the medical industry, precision CNC machining is used to manufacture a wide range of surgical instruments and tools that are critical for successful surgical procedures. These instruments include scalpels, hemostats, drills, and other specialized tools that are used during surgeries to help achieve the desired result.
Precision CNC machining allows for the creation of these instruments and tools to have consistent, precise dimensions and angles, which helps ensure accurate placement and reduces the risk of complications during surgery.
Contact Us to Build Your Custom Medical Device Prototypes and Medical Parts
With a focus on manufacturability and cost-effectiveness, we help you find solutions for medical device development from concept to production.
3D Printing Drives Innovation in the Medical Industry
One of the most significant applications of 3D printing in medicine is the rapid prototyping of surgical implants. By using computer-aided design (CAD) software, surgeons can create precise models of their desired implant before it is even manufactured. This reduces the risk of complications during surgery and ensures better accuracy and fit for the patient.
Another area where 3D printing has made an impact is orthopedic surgery. With its ability to create customized implants and prostheses, doctors are able to provide patients with more accurate and functional solutions. For example, a surgeon may use 3D printing to create a custom bone graft or artificial joint that fits perfectly into the patient's anatomy.
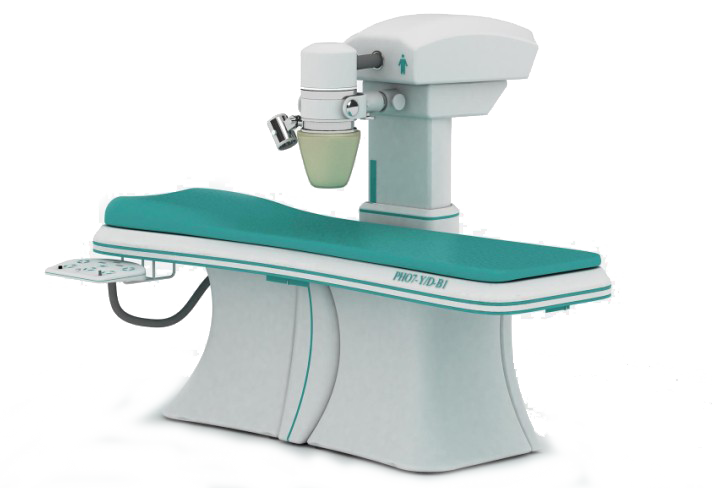
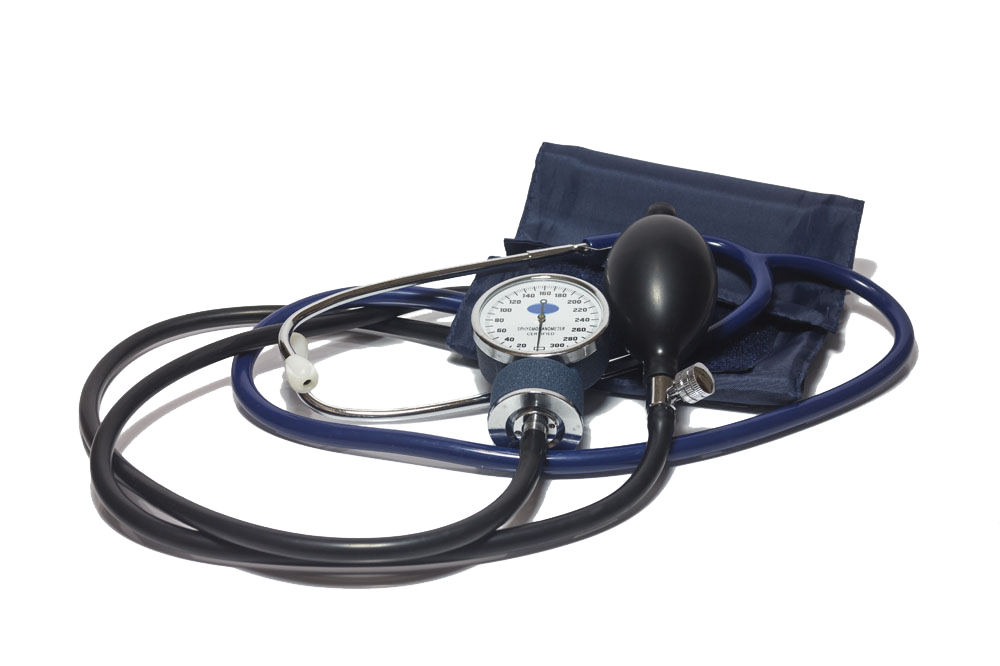
Urethane Casting for Small-scale Rapid Manufacturing in Medical Devices
Urethane casting is a process used for rapid prototyping and small-scale production of medical devices. It involves casting urethane resin into molds to create physical models or prototypes of the device before finalizing the design. This method allows for quick and cost-effective development of new medical devices, as it eliminates the need for expensive tooling and can produce multiple copies of the prototype quickly.
In the case of medical devices, this technique can be used to quickly develop and test various designs before investing in more complex manufacturing processes.
Rapid Injection Molding for On-Demand Manufacturing of Medical Devices
Rapid Injection Molding (RIM) is a manufacturing process that allows for the production of medical devices and components in a single operation. This process involves filling a pre-made mold with a material, such as thermoplastic or thermosetting resin, and then injecting it with heated liquid plastic to create a solid part.
One of the key benefits of RIM is its ability to produce high-quality parts with consistent accuracy and surface finish. The precise control of the injection pressure and temperature allows for uniformity in the finished product, resulting in parts that are free from defects and have consistent performance characteristics.
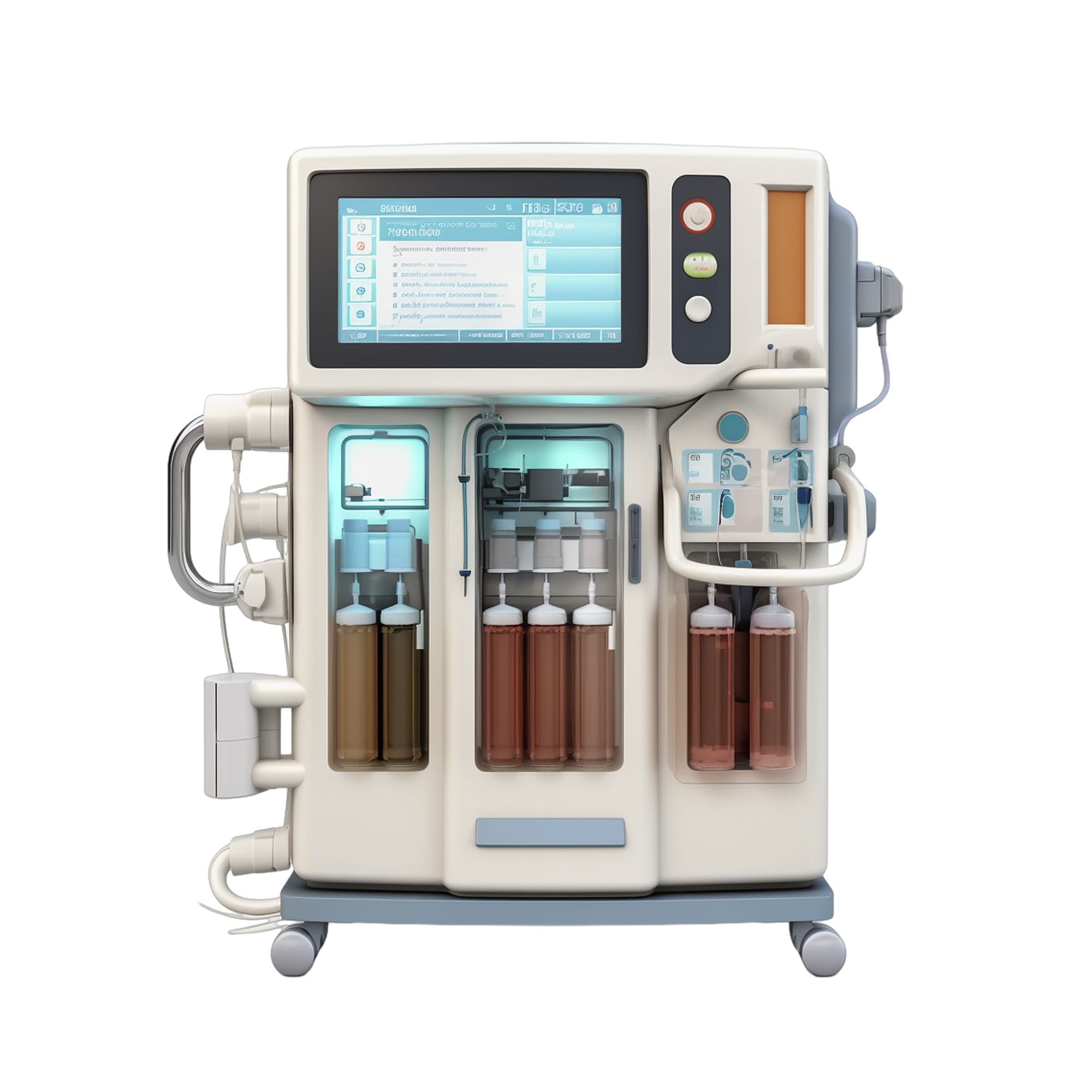
We will work with you to ensure the success of the complete program. Whether you need prototypes, custom devices, or mass-produced components, Oakon delivers reliable and consistent results on time.